Asset Performance Management (APM) is a comprehensive approach that aims to maximize the performance and value of an organization’s assets, including physical assets such as equipment, facilities, and infrastructure, as well as digital assets such as software and data. APM involves a range of activities such as asset tracking, maintenance planning and scheduling, risk management, and predictive maintenance. APM empowers organizations to reduce unscheduled downtime, prevent equipment failure, and reduce maintenance costs while increasing asset utilization, extending equipment life, and identifying underperforming assets.
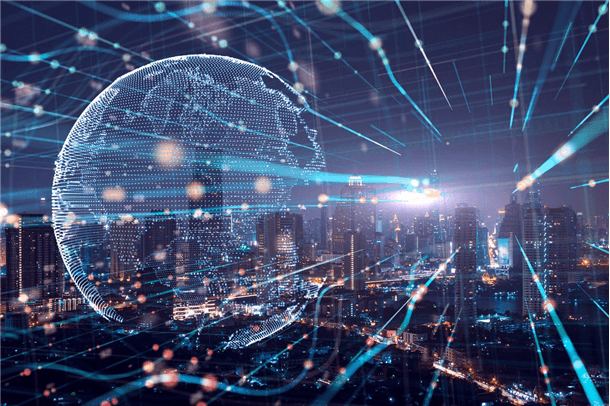
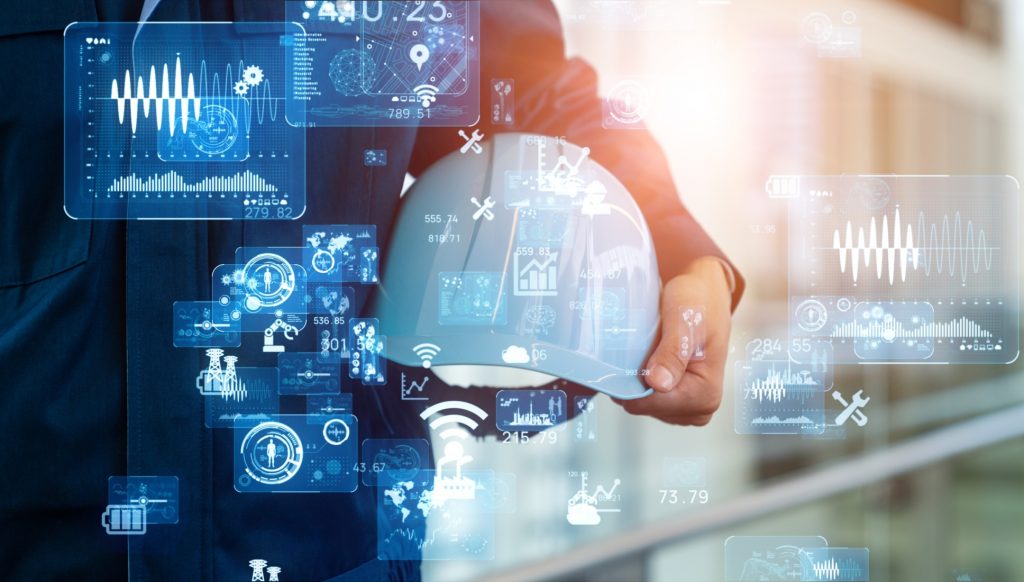
Understand the difference between Condition Monitoring (CM) and Enterprise Asset Management (EAM)
Condition Monitoring (CM) is a subset of APM that focuses on the continuous monitoring of assets to detect early signs of deterioration or failure. CM uses various sensors such as vibration sensors, temperature sensors, and pressure sensors and techniques to collect data on the condition of assets and provides real-time information on their performance. So maintenance teams can take corrective action before a breakdown occurs. It is used for predictive maintenance, and they help maintenance teams to identify potential issues before they become critical, which reduces downtime, maintenance costs and optimizes asset life.
Enterprise Asset Management (EAM) is a comprehensive approach to managing an organization’s physical assets throughout their entire lifecycle, from acquisition to disposal. EAM involves the use of software systems, such as Computerized Maintenance Management Systems (CMMS) to manage asset information, maintenance activities, inventory, procurement, and financial transactions related to the assets. It is a software-based tool that helps organizations manage and plan maintenance activities for their assets. A CMMS provides features such as work order management, inventory control, preventive maintenance scheduling, and asset tracking. It helps organizations to streamline maintenance processes, reduce costs, increase efficiency, and manage their assets more effectively.
How to Maximize Asset Performance with the synergy between Condition Monitoring and Enterprise Asset Management?
Improved Asset Performance
Condition monitoring involves the real-time monitoring of asset health and performance, such as measuring parameters like vibration, temperature, pressure, and more. By integrating condition monitoring data into EAM systems, organizations can gain real-time insights into asset conditions and performance, enabling proactive maintenance and minimizing unexpected failures. This synergy helps optimize asset performance and increase overall equipment effectiveness (OEE).
Predictive Maintenance
By leveraging condition monitoring data within an EAM system, organizations can implement predictive maintenance strategies. Condition monitoring provides continuous asset health data, enabling the identification of early warning signs of potential failures. This data can be used to trigger maintenance tasks, schedule repairs or replacements, and ensure that maintenance activities are conducted at the optimal time, maximizing asset uptime and reducing maintenance costs.
Asset Lifecycle Management
EAM systems facilitate the management of an asset throughout its entire lifecycle, from acquisition to disposal. Condition monitoring data can enhance asset lifecycle management by providing valuable insights into asset usage patterns, wear and tear, and remaining useful life. This information helps organizations make informed decisions about maintenance, repairs, replacements, and capital investments, optimizing asset utilization and extending their lifespan.
Data-Driven Decision Making
Integrating condition monitoring data into an EAM system enables organizations to make data-driven decisions regarding asset management. Organizations can identify patterns, trends, and failure modes by analyzing historical and real-time condition data. This information can be used to optimize asset maintenance strategies, streamline spare parts inventory, allocate resources effectively, and improve overall operational efficiency.
Cost Optimization
The synergy between condition monitoring and EAM can help organizations optimize costs associated with asset management. Organizations can reduce unplanned downtime, minimize costly repairs, and avoid expensive asset replacements by implementing proactive maintenance based on condition monitoring data. Additionally, by utilizing asset health data to plan maintenance activities efficiently, organizations can optimize labour and spare parts costs while maximizing asset uptime.
Integration and Automation
Integrating condition monitoring systems with EAM systems allows for seamless data flow and automation. Condition monitoring data can be automatically captured, analyzed, and incorporated into the EAM system, triggering work orders, generating maintenance schedules, and updating asset records. This integration minimizes manual data entry, reduces errors, and streamlines the overall asset management process.